April 29, 2024
Choosing an ideal tube sealing method can be complicated with all the different types of tubes available. The best option depends on the level of quality you need as well as the type of tube being sealed. Generally speaking, hot air tube sealing is the best option for extruded plastic tubes, laminate tubes, and in-mold label tubes. Aluminum tubes are always sealed with different styles of folds.
Hot Air Tube Sealing
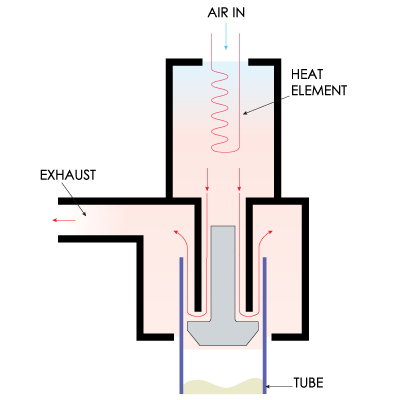
If you are using plastic or laminate tubes and want the most professional seal quality, hot air sealing is the way to go. Hot air sealing is compatible with the largest variety of tubes, and some newer tube materials require hot air to be sealed effectively. Hot air tube sealing also provides the fastest speeds, making it ideal for large production runs. The biggest drawback is the extra cost that comes with additional change parts required to fit each diameter of tube.
To seal a tube with hot air, a special nozzle is dropped down into the tube to heat and soften the inner walls. These nozzles are typically CNC machined from stainless steel; however, we offer an innovative 316L 3D printed nozzle that offers even higher quality seals. Some of the fastest automatic hot air sealing machines will utilize a cooling ring to prevent overheating the tube. After the walls are softened with hot air, the tube moves to the sealing jaw station where it is pressed together and stamped with a batch number or date.
High Frequency Tube Sealing
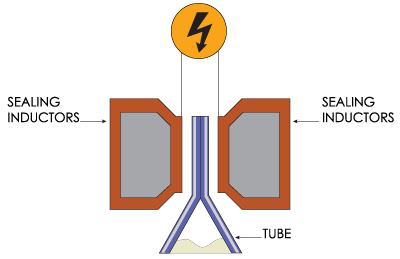
Used only for laminate tubes with aluminum insulating layers, high frequency tube sealing has several limitations. The time to seal a tube with high frequency sealing is much longer than with hot air. In addition, the visual appearance of the final seal is not up to professional quality standards.
High frequency tube sealing works by creating an eddy current in the aluminum tube layers between the inductors. This magnetic field “cooks” the outer layers of the tube until they reach the necessary temperature. Once the melting point is reached, the tube is squeezed together to form the seal.
Ultrasonic Tube Sealing
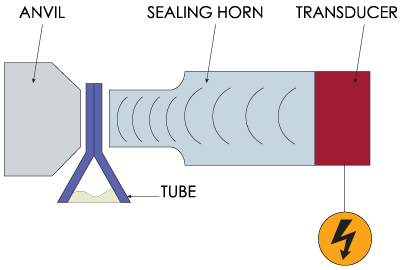
Ultrasonic tube sealing is another budget-friendly option like high frequency sealing. Unlike high frequency sealing, laminate tubes with metal layers are very difficult to seal with ultrasonic sealing jaws. In-mold label tubes also have poor seal quality when using this method due to their polypropylene construction.
Ultrasonic tube sealing machines use a horn or jaw that creates heat with ultrasonic vibrations. The ultrasonic jaw presses the tube closed against an unheated anvil and vibrates to melt the plastic. The pressure against the anvil completes the seal regardless of any product contamination in the sealing area.
Hot Jaw Tube Sealing
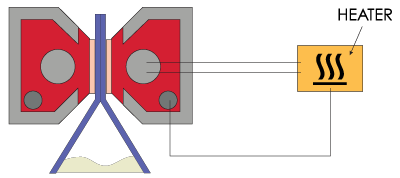
Hot jaw tube sealing is one of the cheapest and simplest ways to seal a plastic tube. With cheap and simple, you also get subpar results in terms of seal quality. However, hot jaw tube sealers are a good low-budget option to test small batches.
The tube sealing process here is rather self-explanatory. Two sealing jaws press the tube closed while heat is applied via convection through the jaws. The tube must sit under pressure and heat for a short time to achieve a full seal, making this one of the slowest sealing options.
Aluminum Tube Crimping
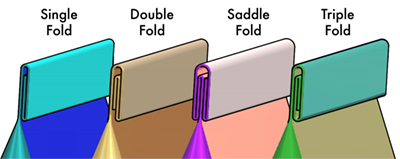
When sealing aluminum tubes, it is most efficient to fold or crimp the tube closed. There are various styles of fold that can be used depending on the desired seal strength and aesthetic. For example, a viscous product will create lots of pressure inside the tube when squeezed, so a stronger fold such as a saddle or triple fold should be used.
To form an aluminum tube seal, the tube must go through a series of folding or crimping stations. Each station uses a set of folding jaws to complete different steps of the fold. Complex folds require more crimping stations and additional length on the tube body compared to a simple single fold. Take a look at our tube holders optimized for aluminum tube sealing here.
Feel free to reach out and contact us with any questions.